
Backstrap Weaving in Peru
Traditional weaving is an incredibly important component of identity in the high Andes, along with traditional alpaca herding and the use of the native Quechua language. Since Quechua was originally an oral language, weaving was the means by which people communicated their thoughts and feelings about the natural world, how stories were told, and histories recorded. Woven textiles were an important measure of wealth, and played a central role in civil and religious ceremonies. Everything from the spin of the yarn and the symbols woven into the textiles, to the colors used and techniques employed, conveys a wealth of meaning about the weaver and where she came from.
WHAT IS WEAVING?
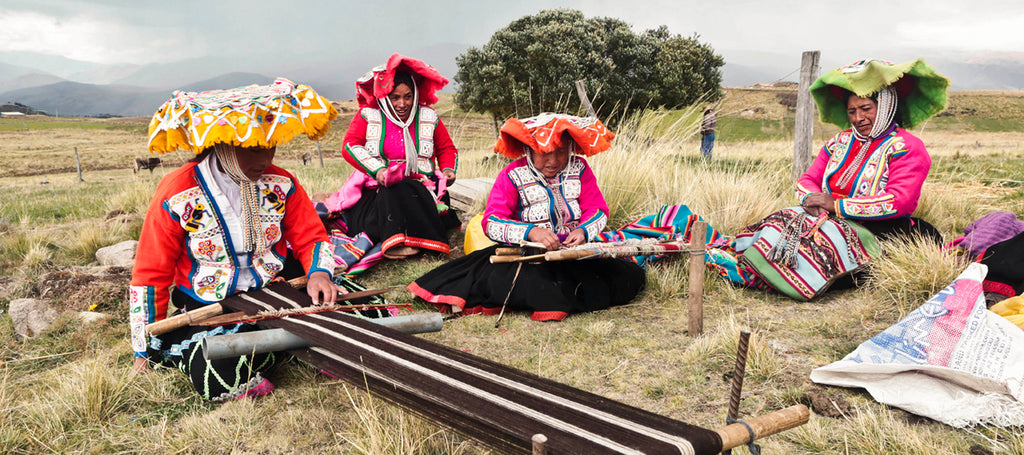
The Backstrap Weaving Loom
In the Andes, traditional Quechua backstrap weaving uses the backstrap loom, the oldest form of loom in the world. An entirely non-mechanized instrument, it is constructed with wood, bone, and strings, and is easily portable from home to field, wrapped inside the traditional lliqlla or manta (carrying shawl) that every woman wears.
...it is the warp that determines the visible color, structure, and artistic character of the piece.
Left: A diagram of a simple backstrap loom, based on the wonderful illustration in the book Guatemalan Textiles Today, by Marylyn Anderson, page 52. Note that there are very few yarns here, and the heddles are greatly oversized for illustration purposes.
The backstrap weaving loom is an elegant tool in its simplicity, effectiveness, and portability. The loom is made up of nine core parts, with a certain amount of variation depending on region and the needs of the specific project. The warp is wound between two warp bars (B and H), one at each end, either singly, for plain areas, or in pairs, in areas of the weaving which will be patterned. A rope (A), is attached to both ends of one warp bar (B), which is simply a heavy piece of wood; the rope is secured to a post or other stationary object. The backstrap (I) is fastened to the other warp bar and passes around of the back of the weaver, who usually kneels on the ground to weave. By moving her body, the weaver can control the amount of tension in the warp yarns throughout the weaving process.
The t’oqoro or shed string (C) helps to keep the yarns of the loom from tangling when this portable loom is set up or taken down, and is also for changing the shed. The shed is created using the shed stick (D) and the heddle stick (E). The heddle stick (illawa in Quechua) is wound with string loops (heddles) that reach down through the top yarns and loop around each of the bottom yarns of the warp.
When the weaver lifts up on the heddle stick, the bottom yarns are pulled up above the top yarns, creating a shed. With the appropriate set of warp yarns raised, the weaver then, deftly and with incredible speed, picks up certain warp yarns and lets others drop, using either her fingers or a thin wooden tool. This selection of warp yarns creates one row of the woven pattern in the textile.

The weaver then passes the weft or mini through, using a shuttle or bobbin (G). Once the shuttle has passed through, the batten (F) is used to push the horizontal weft thread into place. The weft is further beaten into place using a small pointed bone tool called a r’uki (the beater (J). The beating process does a great deal to determine the density of the overall finished product.
At this point, the shed is changed by pulling the shed stick back toward the weaver, pushing the bottom yarns back down below the top yarns. The process is repeated, picking up and dropping warp yarns and securing them with the weft, as another line of the pattern is created. The warp bar closest to the weaver (H) is used to roll up the completed portion of the weaving, keeping it out of the way.
Four-Post Loom
The four-post loom is a form of a horizontal loom in which four stakes or posts are hammered into the ground in a rectangular arrangement.
The warp beams are secured to the posts across the short ends of the rectangle, using woven straps. The warp is thus suspended with tension, parallel to the earth, and the weaver sits at one end on the ground and works from there. The four post loom can be modified into a six post arrangement, which allows the weaver to set up two interlocking warps, each with a separate color design. Known as discontinuous warp weaving, this is an extremely difficult and little-practiced weaving technique. A combination of the four-post and backstrap techniques uses two posts to secure one end of the warp, while a back strap secures the other around the weaver, who sits on the ground and applies tension from there.
The Warping Process
Warping a textile involves two people. If the warp is being constructed horizontally, then four posts will be set in the ground: the corner posts of a rectangle. These will be placed at distances that reflect the intended size of the finished weaving. On the short ends of the rectangle, a warp bar will be secured horizontally, forming the ends of the warp. Balls of yarn are then tossed back and forth by the weavers sitting at either end. Each time a ball of yarn is passed, it is wrapped around the warping bar. For areas of design or pallay, two balls are tossed at a time in order to create the “pair” of warp yarns necessary for forming the design. This process is repeated until all the warp yarns are laid, in the correct order, and the weaving process is ready to begin.
If the warp is to be created vertically, then two posts will be placed in the ground at a distance that reflects the final length of the piece; the height of each post will determine the width of the warp. The warping is laid in essentially the same manner, tossing balls of yarn back and forth and wrapping them around each post.
Warping can take hours, but it is a social process which often involves a lot of conversation. Much of this conversation revolves around decisions of color and pallay. These decisions set the overall artistic palette for the weaving. Warping is generally a positive and animated activity - full of promise and anticipation!
Weaving Techniques
The vast majority of Andean weaving is warp-faced, in which the weft yarns are completely hidden by the warp during the weaving process. As a result, it is entirely the warp which determines the visible color structure and artistic character of the piece. There are several warp-faced weaving techniques common in the Andes:
Complementary warp technique creates a pattern which appears as a positive on one side, and a negative on the other. For example, a black river on a white background on one side shows as a white river on a black background on the other side. This is the most common weaving technique in the high Andes.
Supplementary warp technique involves creating a pattern that sits on a background color and appears on only one side of the fabric. This technique involves the introduction of an additional set of warp yarns which are used to create the pattern but are not integral to the structure of the weaving itself. It is a more difficult and much less common technique.
Discontinuous warp technique allows a weaver to create patterns within the warp that change along the length of the fabric. One way to create such a warp is with a six-post horizontal loom (described above, under Looms). This allows the weaver to interlock two separate warps, each sharing the middle warp bar. Weavings produced with this technique are incredibly complex and beautiful. Currently, this technique is disappearing and is only commonly practiced in one region.
Weft-faced weaving techniques, such as tapestry (tapiz in Spanish), allow the weaver to create intricate patterns using the weft yarns. Tapestry is usually created on a fixed loom frame, with work proceeding from bottom to top. This is a technique often practiced by men, and is relatively uncommon in comparison to warp-faced techniques.
Weft-faced techniques are also employed in the creation of golón, the highly colorful trim seen adorning many of the women’s traditional skirts or polleras. This technique is very complex and time-consuming, and requires many small shuttles, each carrying different color yarns.
Finishing
The way a weaving is finished can play an enormous role in the overall quality of the completed work. Finishing provides the final touches that communicate a sense of care and attention to detail. There are many finishing techniques for the different types of products: below we present just a few:
a. Chukay is the technique of stitching two smaller woven pieces together using embroidery stitches. b. This runner has gorgeous yarn fringe. c. This chuspa features a woven edge, which has been finished in a yarn fringe before being sewn onto the bag d. Another chuspa is finished in a wide yarn fringe. e. A runner with a diamond pattern edging (called ñawi awapa), which is woven separately, then sewn on. f. This bracelet is finished with beaded edges.